2020年度省エネ大賞 受賞内容のご紹介
当社は、草加工場における品質の維持と省エネを両立させる取り組みにより、2020年12⽉21⽇に発表された2020年度省エネ⼤賞(主催:⼀般社団法⼈省エネルギーセンター)の省エネ事例部⾨ において、最⾼賞にあたる「経済産業⼤⾂賞」を受賞しました。ここではその取り組みの具体的な内容についてご紹介します。
省エネ大賞受賞のお知らせはこちら(0.423 MB)
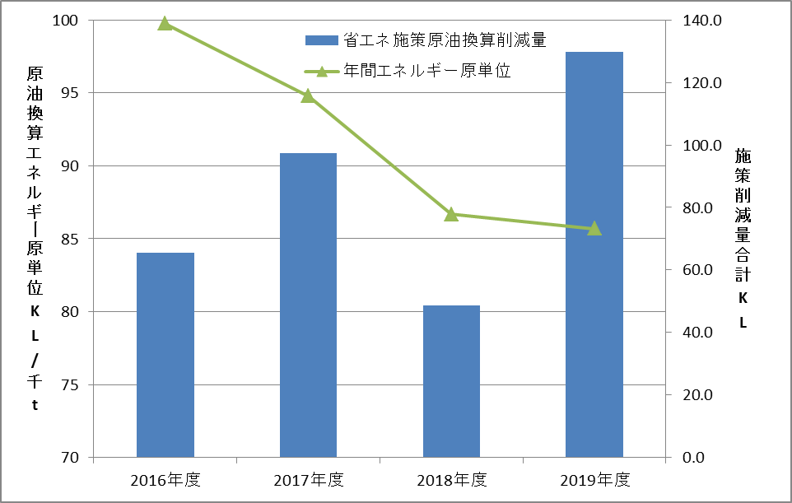
【ポイント】
- 食品製造業は品質に対する要求事項が多く、品質に関与するエネルギーの省エネは進みづらかった
- 当社草加工場では、省エネ委員会の組織改革を通じてそれら品質に関与するエネルギーの省エネを実現した
- この取り組みにより、5年間で25%以上のエネルギー原単位の削減に成功した
(2014年度116kL/千tから、2019年度86kL/千tまで削減)
食品製造業は一般的に省エネが進みにくいと言われています。その理由の一つとして、食品業界では品質に求められるレベルが高いことが挙げられます。
食品は人が口に入れるものですから、菌の繁殖や異物・アレルゲンの混入といった健康被害につながる品質不良は絶対に許されません。その結果、洗浄や殺菌、工場内環境の管理といった品質に関与する部分については条件を変更することのハードルが高くなり、省エネ活動の手が及ばない「聖域」のような扱いになってしまうことも少なくありませんでした。
一方で、食品製造における洗浄や殺菌では食の安全のために薬品ではなく熱を使う場合が多いなど、品質の維持のために消費されるエネルギーは決して小さくありません。そのため、こうした「聖域」の存在は食品製造業の省エネの難易度を高める大きな障害となっていました。
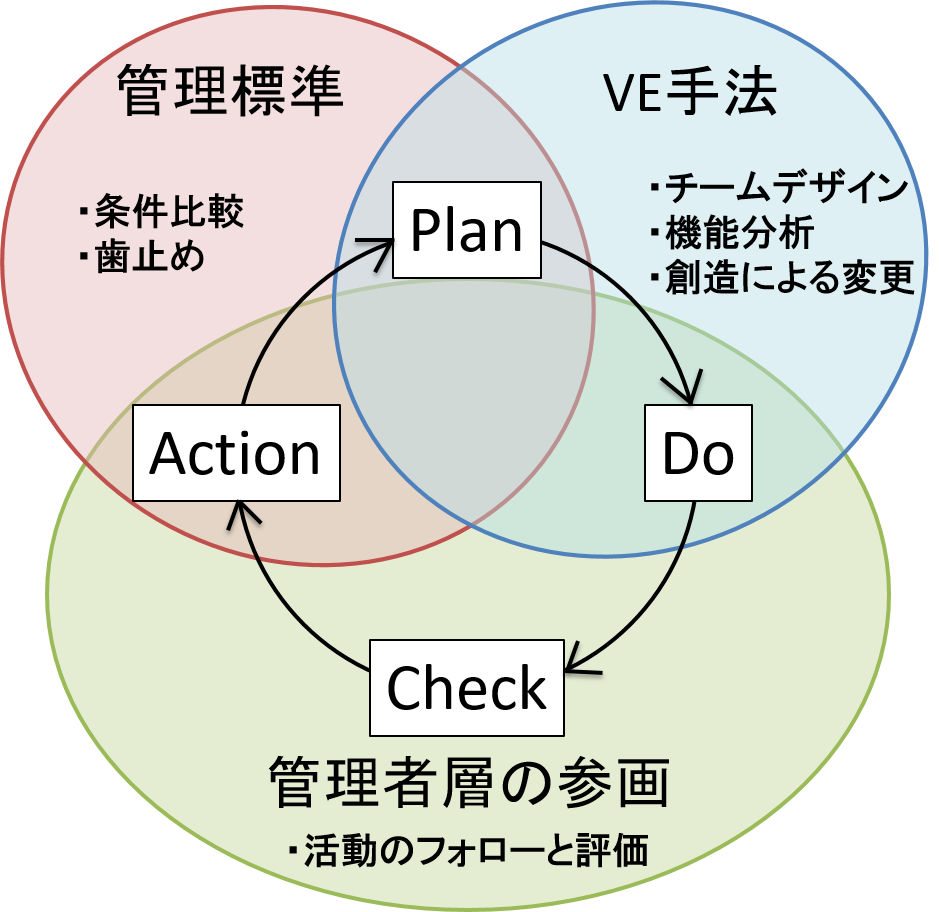
当社は2006年に省エネ委員会を立ち上げて省エネ活動を推進してきましたが、品質に関与するエネルギーの省エネは、施策の実現に向けて必要な知識が異なるだけではなく、品質管理部門の了承も得なくてはならないため、従来の組織では対応が困難でした。そこで、草加工場では「聖域」の省エネを進めるため、省エネ委員会の組織改革に着手しました。
具体的には、PDCAの各工程において問題点を抽出し、対応策として①VE(Value Engineering:価値工学)手法の取り込み、②係対抗省エネプレゼン大会の開催、③管理標準の活用を実施することで、「分科会で品質と省エネに関わる議論を通じて立案」「品質管理部門と連携し品質面を担保」「管理者層への成果プレゼンによる評価確立」「管理標準活用による歯止めと水平展開」という活動サイクルを確立しました。
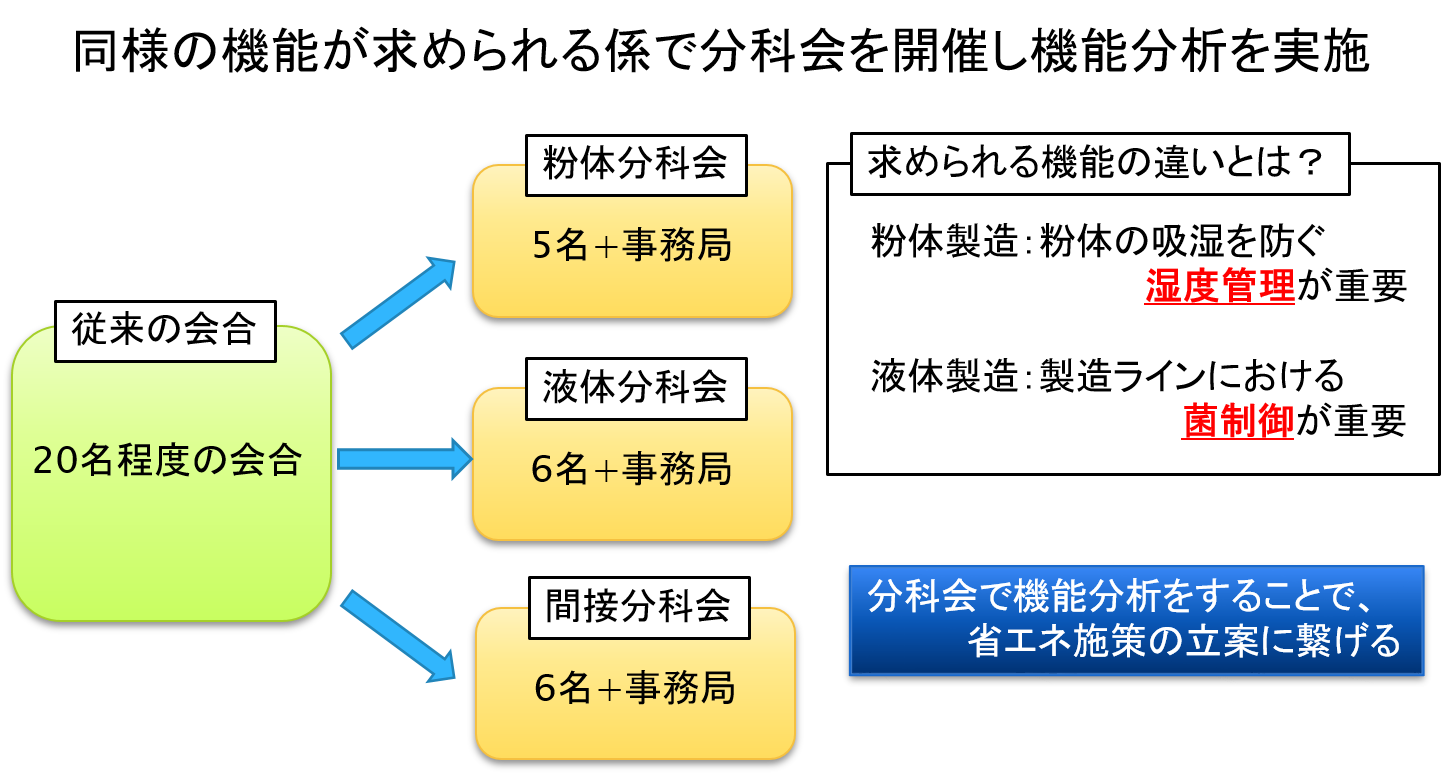
a.分科会の開催
委員会の会合形式を分科会に変更し、品質に関わる工程や設備の機能分析を通じて省エネ施策の立案を実施しました。分科会は品質の維持に必要な機能が近い部門の委員を集めて粉体分科会と液体分科会に区分し、品質に関わる議論を行いやすくしています。
b.品質管理部門との連携
分科会で立案した施策について品質管理部門と意見交換し、テストを実施したうえで実行することにより、品質を担保した省エネ活動を実現しました。
c.教育の強化
固定観念にとらわれない柔軟な発想をするには土台となる省エネ知識が必要不可欠なため、エネルギー管理員講習の受講による基礎知識の強化と、エネルギー診断プロフェッショナル資格の取得による応用知識の強化を推進しました。
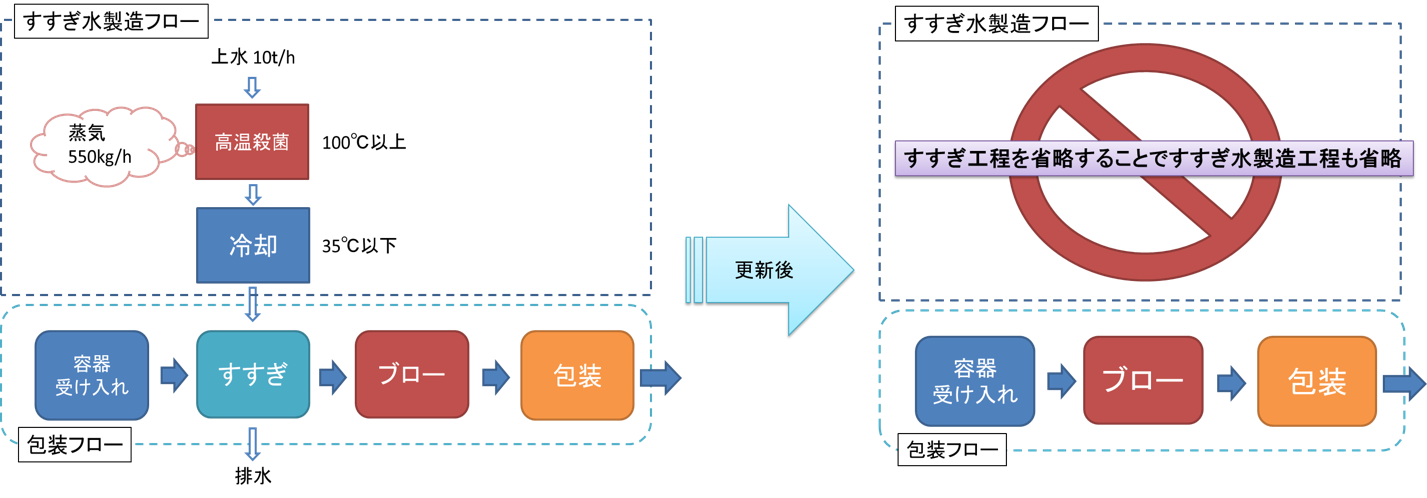
従来、調味料の包装ラインでは容器のすすぎ工程に用いるすすぎ水の高温殺菌および冷却に多くのエネルギーを消費していましたが、分科会で議論を重ねるとともに、機械メーカーや容器メーカーとプロジェクトチームを形成し、洗浄方法を変更することですすぎ工程の省略に成功しました。 この結果、製造1時間当たり550kgの蒸気を削減し、原油換算で年間約40kLのエネルギーを削減しました。
液体分科会での情報共有により、液体製品の製造開始前にタンクと付帯配管の殺菌に使用する熱水の量が係によって異なることが判明しました。そこで、品質管理部門と協力して水量を変更した場合の殺菌効果について検証しつつ最適化を図った結果、弁の交換や流量調整を実施することで、必要な熱水の量を2/3程度まで削減することに成功しました。 この施策は広く水平展開が可能であったため、累計10基のタンクで同様の施策を実施し、年間約4,400m3の都市ガス削減に繋がりました。
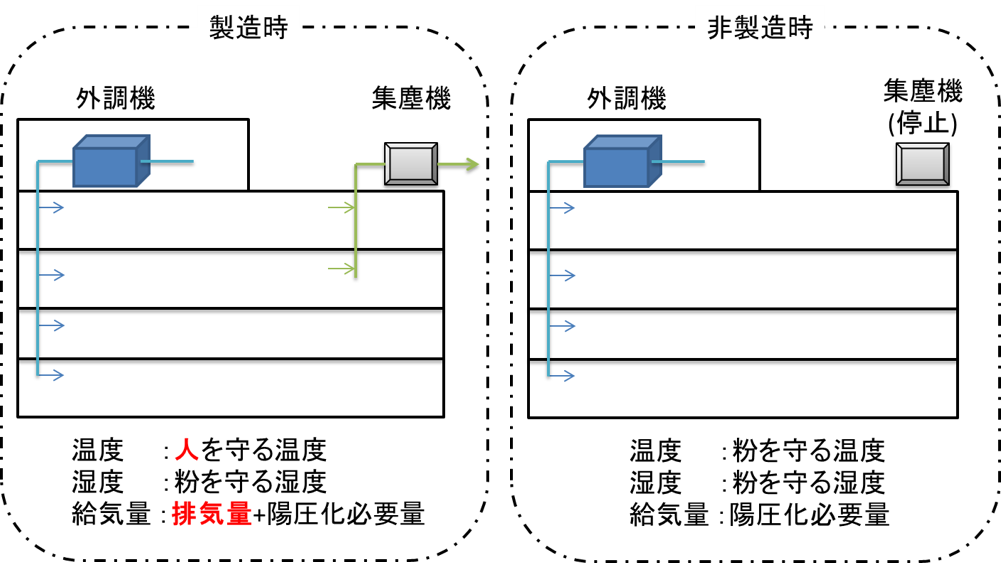
従来、粉体工場では建屋全体の陽圧化のため24時間365日定温定湿の給気条件で外調機を稼働させていましたが、製造時と非製造時では必要な機能が異なっていることがわかり、非製造時の給気温湿度条件と給気量の調整を行いました。 この結果、年間で電力約67,000kWh、都市ガス約4,300m3を削減することができ、原油換算すると約22kLの削減となりました。
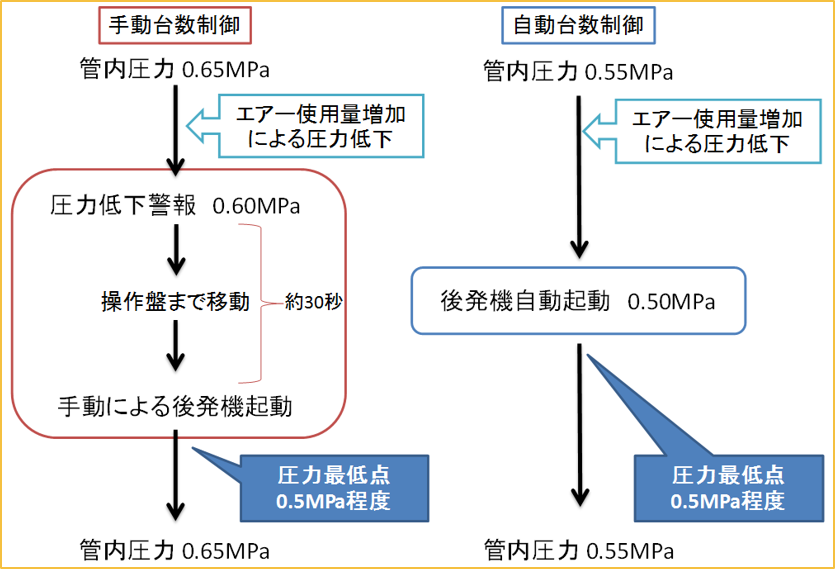
管理標準から全製造現場のコンプレッサー効率を確認したところ、大きくばらつきがあることが判明したため、供給側・消費側の両面で省エネ施策を進めました。
例えば供給側の施策としては、台数制御を手動から自動に変更し、吐出圧を下げコンプレッサー効率を19%改善した結果、年間26,000kWhの電力削減となりました。
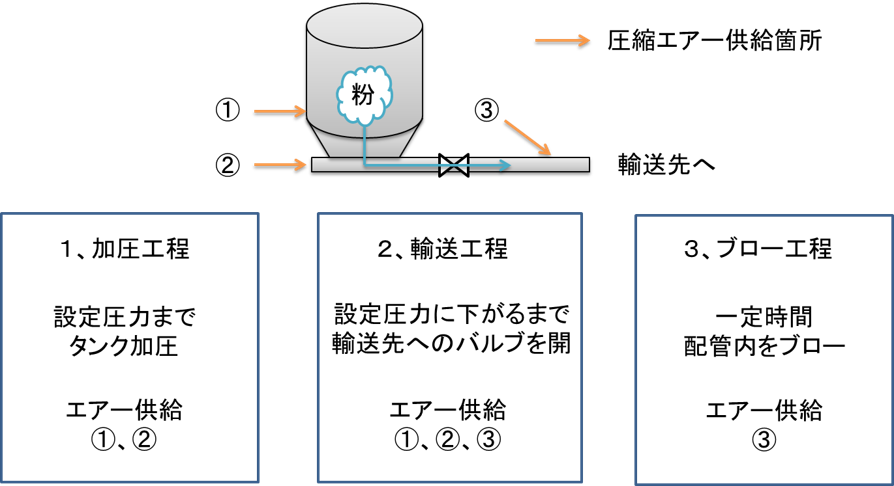
また、消費側の施策としては、導入から30年間調整されず聖域化していた空気輸送装置の条件を変更し、1輸送当たりに消費するエアー量を87.8Nm3から55.4Nm3と約37%改善しました。輸送作業は年間7,000回以上実施しているため、コンプレッサー消費電力を年間約45,000kWh削減することができました。